Reducing CO2 emissions twice over
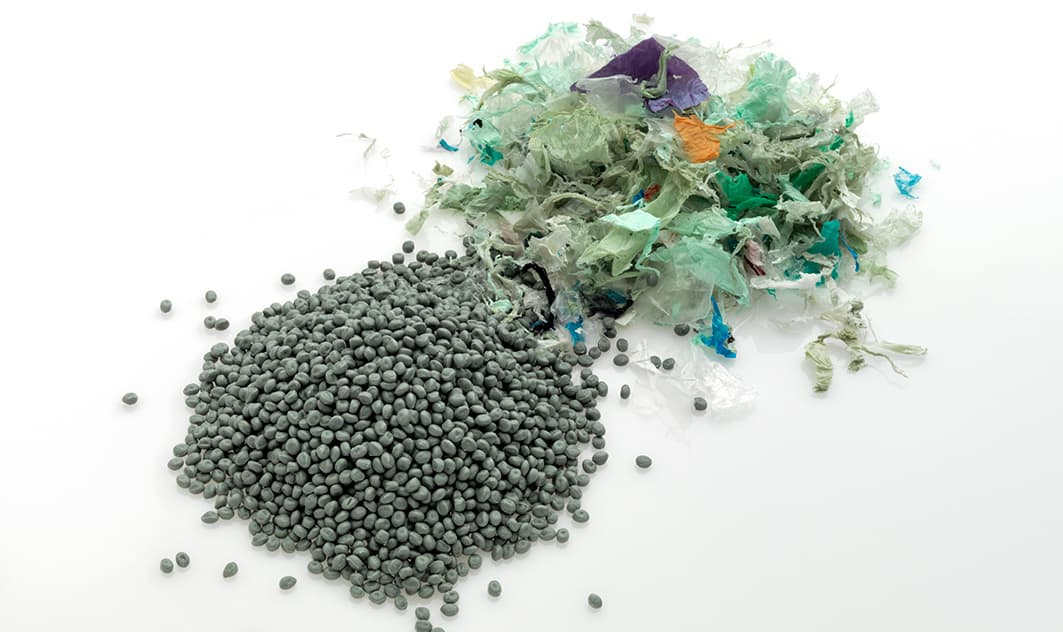
Thermoplastic foam injection molding with post-consumer recyclate
Foam injection molding inherently saves material. And it gets even better: How about using post-consumer recyclate instead of virgin material in the process to reduce the CO2 footprint even further? In collaboration with the Schmalkalden University of Applied Sciences, KraussMaffei has investigated this question, with particular focus on what this means for the mechanical component properties.
Analyses by KraussMaffei and the Schmalkalden University of Applied Sciences show the effects that result when thermoplastic foam injection molding, specifically the MuCell process, is combined with the use of post-consumer recyclate (PCR).
The test arrangement combined requirements of the highest difficulty because the foamed component was to weigh up to 12% less than the compact one and be made from 100% recycled granules. This comes from processed post-consumer waste (PCR) and is therefore significantly more contaminated and less homogeneous in terms of material characteristics than single-variety recyclates from industrial waste (PIR).
Do the negative influences add up?
Recycled material from post-consumer waste has often undergone a stressful reprocessing process in which it was melted in an extruder; in the process, the plastic is always negatively affected by shear forces and thermal stress. For the use of such recycled material in the MuCell process, it was therefore necessary to clarify whether the two effects add up. In addition, the electrical properties were to be analyzed in cooperation with an industrial partner.
Please log in to read the full article
All our content is free and accessible after logging in. You can register for a free account below.