The winners of the prestigious Innovation Award for Fibre-Reinforced Plastics of the AVK, the German Federation of Reinforced Plastics, were presented in Salzburg this year. This award always goes to businesses, institutions and their partners for outstanding innovations in composites the three categories Products & Applications, Processes & Methods and Research & Science. Projects are submitted in all three categories and are evaluated by a jury of experts in engineering and science as well as trade journalists, who look at each project in terms of their levels of innovation, implementation and sustainability.
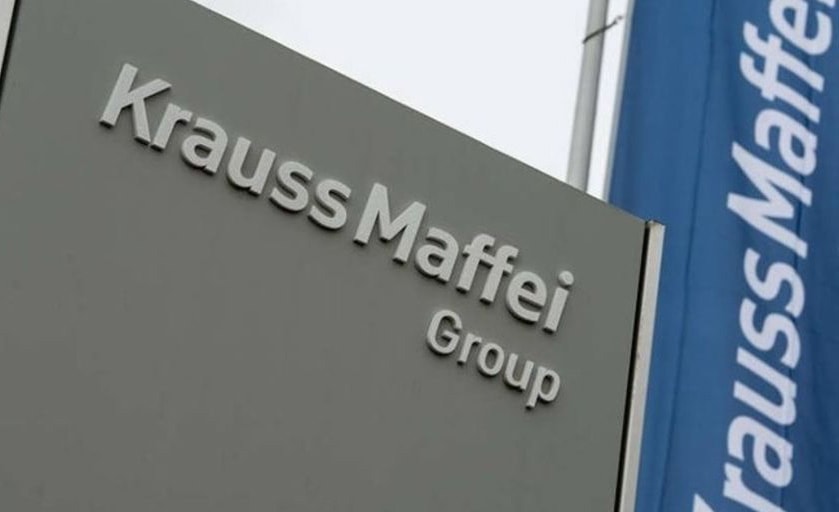
KraussMaffei and Wirthwein win AVK Innovation Award
First place in Processes & Methods went to KraussMaffei Technologies GmbH and its partner Wirthwein SE for their “Chopped Fibre Direct Process (CFP)”.
This innovative direct fibre-processing method, CFP, will transform the fibre processing into injection-moulding machines. Being efficient and simple, it saves up to 46% in material costs and 0.8 kWh/kg in energy, as it eliminates the need for pre-compounded materials. By using a standard injection moulding machine and a patented screw, CFP significantly reduces production costs. All that needs doing is some adjustments to the material feed and the screw. CFP has reached TRL 8 and has also been successfully tested in automotive injection-moulding applications. The new screw design allows cost-effective retrofitting of existing machinery, replacing expensive continuous-fibre processes. The patented screw geometry also permits direct processing of waste materials from other production processes, such as PA-CF waste from the aerospace industry, without the need to separate fibres and polymers. The new process, CFP, promises quality, efficiency and sustainability.
Second place went to the Fraunhofer Institute for Manufacturing Engineering and Automationand its industrial partners Schindler Handhabetechnik GmbH and Vision & Control GmbH for their “CIRC (Complete In-House Recycling of Thermoplastic Compounds)” process.
Together, they developed an innovative process for the efficient use of offcuts from the processing of thermoplastic organic sheets. Current recycling processes have so far led to the loss of fibre-composite structures and thus also of the high mechanical strength associated with them. The new process captures the geometry and material data of offcuts, combines them efficiently and consolidates them into a new organic sheet via a thermoforming process. Besides a high recycling rate, this also ensures that the relevant mechanical properties are largely retained. The process thus promises a more sustainable and cost-efficient use of organic sheets by minimising waste, while also being scalable to suit different types of applications and materials.
Third place went to CarboScreen GmbH together with the Institute of Textile Technology at RWTH Aachen University for “CarboScreen – Sensor-Based Monitoring of Carbon-Fibre Production”.
Carbon fibres are among the most important lightweight construction materials. They are made through the thermal conversion of a PAN fibre. The manufacturing process is highly complex and sophisticated. At present, it is only monitored visually in the industry, by semi-skilled staff. However, inadequate process control can lead to fibre damage and, in extreme cases, to production line fires that are often not detected early enough. To ensure satisfactory product quality, the maximum production speed is limited to 15 metres per minute, which considerably reduces the production capacity of a plant. To improve and accelerate the manufacturing process, CarboScreen GmbH, a company founded under an EXIST grant, now offers a sensor-based monitoring system for carbon fibre production. The underlying technology allows the continuous monitoring of fibres during production and automatically identifies any deviations.