In today’s global economy, there is an immediate need for producers to address the challenges of evolving markets while driving more sustainable practices. A leading North American producer of sustainable packaging handles for the food, beverage and consumer goods industries required a heavy-duty, high-performance injection molding solution to support mass production of plastic handles made from 100% recycled HDPE and using multi-cavity molds. The challenge was delivering a solution that could manage the demanding output, productivity and quality requirements, while effectively processing recycled material to embrace the principles of circular economy.
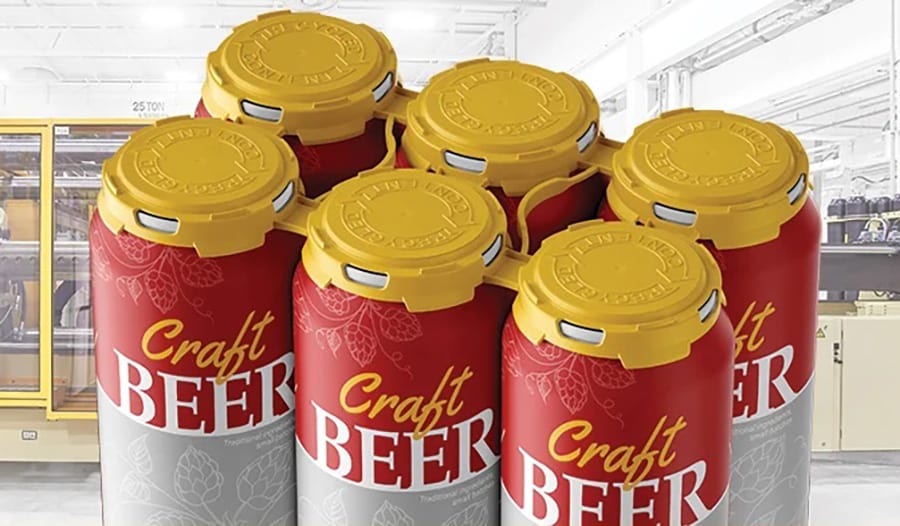
100% Recycled HDPE handles from Husky
To produce this customer’s handles for canned beverage applications, Husky proposed their high performance Hylectric machine platform. The Hylectric machine’s unique Reflex platens provide uniform clamp force distribution to deliver better part quality, reduce scrap and extend tool life. The system is also designed with optimized screw geometry for more efficient processing of recycled resin, and melt stream delivery components, including screw, barrel and check valve, are built with specialized high wear resistant materials to improve the handling of recycled material and increase equipment longevity.
RESULTS
Husky’s Hylectric system has yielded several significant ongoing performance, productivity and sustainability improvements for this customer. Combined with Husky hot runner systems, also optimized for recycled resin processing, Hylectric machines provide optimum performance, part quality and reliability results on long-term runs. By incorporating recycled material, this producer has been able to significantly reduce their carbon footprint and now generates 78% fewer greenhouse gas emissions, consumes 90% less energy for reduced production costs and uses 100% less petroleum when compared to virgin HDPE. In addition, their handles made from 100% recycled material are recyclable for future conversion into new handles or other applications and by phasing out virgin raw material they have been able to significantly reduce parts costs.
Please log in to read the full article
All our content is free and accessible after logging in. You can register for a free account below.